Technical Hub Flooring Wear Resistance
It is important to understand the complexities involved with testing the wear resistance of a product.
Wear Resistance
Whilst almost all formal testing for wear resistance is carried out using a taber abrasion machine, different testing methods and varied testing environments can have different effects on the outcome of the testing.
Firstly, the taber abrasion machine is used across the world to test the abrasion resistance or wear resistance, of different types of flooring surfaces.
Sometimes an abrasive wheel is used to grind away at the sample to determine how many grams of coating or surface were lost after a defined number of revolutions. Other tests involve “scuffing” away at the surface with a leather wheel until the coating shows pre-determined signs of wear. In some tests, sand is ground into the sample by the leather wheel and in others the leather is swapped for a specified grade of sandpaper that will wear away at the sample until a specified point of wear is achieved. Different countries have different standards and different companies perform different tests in order to maximise their products results using one particular testing method.
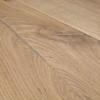
To add further confusion to the issue, the relative humidity and temperature at the time of testing as well as, in some cases, the chemists interpretation of results can also have an influence on these results. In all, the important thing is that when comparing products in terms of wear resistance we must make sure that we are comparing apples with apples. We need to make sure that, at very least, the results being compared were provided by a reputable laboratory and were achieved using identical testing methods.
The Quick-Step Test Method
The method used to determine the wear resistance fo Quick-Step is in line with the test procedures prescibed by the European Standard EN13329. It involves the use of a specified sandpaper on the taber abrasion machine. The sample piece spins, being abraded by the sandpaper, until the patterned design layer begins to show signs of wearing through. This stage is known as the Initial Point (IP) of wear and is very clearly defined by the standard, leaving little to interpretation by the testing authority. The sample is viewed every 100 revolutions and the abrasive paper is changed every 200 revolutions. The number of revolutions required to reach this stage is recorded and the sample is then given an Abrasion Class ranging from AC1 to AC5, with AC5 being the most wear resistant class.
In some tests, the wheel resumes spinning until almost all of the design layer has been worn through. This point is referred to as the Final Point (FP) of wear. In these tests, the IP and the FP are then added together and divided by two to determine the AT, or Average Taber. For marketing purposes, the AT is often the figure expressed when reporting on the wear resistance of a laminate floor.
How Quick-Step Performed
Like all products, Quick-Step varies slightly from batch to batch. Despite slight variations from batch to batch, Quick-Step achieves an AC4 rating (Impressive Ultra achieves AC5) in accordance with EN13329 and has an Average Taber (AT) between 10,500 and 11,000 when tested in accordance with EN 438-2,6.
If you still need convincing that Quick-Step is extremely wear resistant, ask your local Premium Office for the details of some commercial installations in which Quick-Step has been installed. Hundreds of high traffic commercial installations across Australia serve as testament to Quick-Step’s wear resistance.
It is very important however to balance wear resistance with other important factors when making a purchasing decision. Joining systems, moisture resistance of the fibreboard core, indentation resistance and warranty information should all be factors that influence any purchasing decision for laminate flooring.